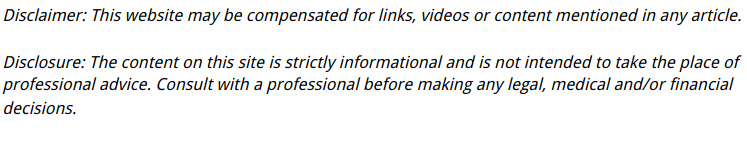
Manufacturing companies, whether they specialize in stainless steel clamps or intrinsically safe barriers, rely on sound financial management to drive growth and sustainability. From budgeting and forecasting to cost control and risk management, manufacturers must make informed decisions to optimize their financial performance. In this article, we delve into the key financial strategies that top manufacturers employ to stay ahead of the curve and thrive in today’s competitive landscape.
1. What Financial Strategies Do Top Manufacturers Employ?
Manufacturers, regardless of their specific industry focus, must prioritize effective budgeting and forecasting to support strategic decision-making and ensure financial stability. By developing detailed budgets and accurate forecasts, companies can proactively identify potential financial challenges and opportunities, allowing them to make timely adjustments to achieve their goals. From heavy equipment sales to rebar fabrications, manufacturers must allocate resources wisely and monitor performance closely to stay on track.
Investing in technology is a key strategy that top manufacturers use to streamline operations, enhance productivity, and drive innovation. From implementing advanced robotics and automation to adopting cutting-edge ERP systems, companies can leverage technology to improve efficiency, reduce errors, and accelerate growth. By embracing digital transformation and staying abreast of the latest technological trends, manufacturers can stay ahead of the competition and achieve sustainable financial success.
2. How Do Manufacturers Maintain Cash Flow?
Cash flow management is a critical aspect of financial strategy for manufacturers, as maintaining adequate liquidity is essential for meeting day-to-day expenses and investing in future growth. By forecasting cash flow projections and monitoring cash inflows and outflows, companies can proactively manage their working capital and avoid liquidity constraints. Whether it’s managing inventory levels or optimizing accounts receivable and payables, manufacturers must prioritize cash flow management to ensure financial stability.
Strategic inventory management is essential for manufacturers, as excess inventory ties up valuable capital and increases carrying costs, while inadequate inventory levels can lead to production delays and customer dissatisfaction. By implementing efficient inventory control systems and adopting just-in-time manufacturing practices, companies can minimize carrying costs, reduce lead times, and improve overall operational efficiency. Whether it’s maintaining safety stock levels or optimizing reorder points, manufacturers must balance inventory levels carefully to support their cash flow needs.
3. What Role Does Cost Accounting Play in Manufacturing?
Cost accounting is a fundamental practice that manufacturers use to track and analyze production costs, identify cost drivers, and allocate expenses accurately. By leveraging cost accounting methods such as standard costing, activity-based costing, and job order costing, companies can enhance cost visibility, improve decision-making, and drive operational efficiency. Whether it’s calculating production costs for stainless steel clamps or analyzing manufacturing overhead for high-pressure hermetic seals, cost accounting provides valuable insights into the cost structure of a manufacturing business.
Activity-based costing is another cost accounting method that manufacturers use to allocate indirect costs to products based on the activities required to produce them. By identifying cost drivers and tracing costs to specific activities, companies can accurately allocate overhead expenses and determine the true cost of production. Whether it’s allocating overhead costs for concrete grinders or analyzing cost drivers for hitches, activity-based costing provides manufacturers with valuable insights into the cost structure of their operations and helps them make informed pricing and production decisions.
4. How Do Manufacturers Manage Financial Risks?
Financial risk management is a critical aspect of financial strategy for manufacturers, as companies face a range of risks that could impact their profitability and sustainability. By conducting comprehensive risk assessments, identifying potential threats, and developing risk mitigation strategies, manufacturers can proactively manage financial risks and safeguard their business. Whether it’s assessing market risks for heavy equipment sales or managing operational risks for rebar fabrications, manufacturers must prioritize risk management to protect their assets and ensure long-term viability.
Contingency planning is another key component of effective risk management for manufacturers, as companies must prepare for potential disruptions and develop response strategies to mitigate the impact of unforeseen events. By creating contingency plans for supply chain disruptions, natural disasters, and other emergencies, manufacturers can reduce downtime, minimize financial losses, and ensure business continuity. Whether it’s developing backup plans for production delays or establishing emergency response procedures for high-pressure hermetic seals, manufacturers must be proactive in managing risks and preparing for contingencies.
5. How Is the Performance of Manufacturing Companies Measured Financially?
Manufacturing companies use a variety of financial metrics and key performance indicators (KPIs) to evaluate their financial performance, monitor profitability, and track operational efficiency. By analyzing key financial ratios, performance dashboards, and benchmarking data against industry standards, companies can assess their performance relative to their peers and identify areas for improvement. Whether it’s measuring return on investment for hitches or analyzing profitability margins for home builders, manufacturers rely on financial metrics to gauge their financial health and make informed decisions.
Key financial ratios such as liquidity ratios, profitability ratios, and solvency ratios provide valuable insights into a company’s financial health and operational efficiency. By calculating ratios such as current ratio, return on assets, and debt-to-equity ratio, manufacturers can assess their liquidity, profitability, and financial leverage. Whether it’s analyzing inventory turnover for concrete grinders or evaluating return on investment for heavy equipment sales, financial ratios help manufacturers benchmark their performance and identify areas for improvement.
Performance dashboards are another valuable tool that manufacturers use to monitor key performance metrics, visualize financial data, and track progress toward strategic goals. By creating customized dashboards that display real-time information on sales, expenses, and profitability, companies can make data-driven decisions and align their resources with business objectives. Whether it’s analyzing revenue growth for fire protection sprinkler companies or tracking production efficiency for rebar fabrications, performance dashboards enable manufacturers to stay informed and agile in today’s dynamic business environment.
6. What Financing Options Are Available for Manufacturers?
Manufacturers have a range of financing options available to fund their operations, invest in growth opportunities, and manage working capital needs. Whether it’s debt financing, equity financing, or alternative financing solutions, companies must carefully evaluate their financing options and choose the most suitable option based on their financial goals and risk tolerance. In this section, we explore the different financing options available to manufacturers and discuss the benefits and considerations associated with each.
Debt financing is a common financing option that manufacturers use to borrow funds for capital investments, expansion projects, and working capital needs. By issuing bonds, securing loans, or establishing lines of credit, companies can access capital to fund growth initiatives and support day-to-day operations. Whether it’s financing equipment purchases for heavy equipment sales or funding new projects for home builders, debt financing provides manufacturers with the flexibility and liquidity they need to thrive in today’s competitive market.
Alternative financing solutions such as invoice financing, supply chain financing, and peer-to-peer lending offer manufacturers additional options to access capital and manage cash flow effectively. By leveraging these alternative financing solutions, companies can address short-term funding needs, improve liquidity, and support working capital requirements. Whether it’s securing financing for metal etching stencils or optimizing cash flow for rebar fabrications, alternative financing solutions provide manufacturers with the flexibility and agility they need to navigate today’s rapidly changing business landscape.
7. How Do Manufacturers Handle Financial Reporting and Compliance?
Financial reporting and compliance are essential aspects of financial management for manufacturers, as companies must meet regulatory requirements, disclose accurate financial information, and provide transparency to stakeholders. By establishing robust internal reporting systems, ensuring regulatory compliance, and implementing best practices for audit processes, manufacturers can maintain financial integrity and build trust with investors, lenders, and other stakeholders. In this section, we explore how manufacturers handle financial reporting and compliance to ensure transparency and accountability in their operations.
Internal reporting systems play a critical role in enabling manufacturers to track financial performance, analyze key metrics, and make data-driven decisions. By implementing accounting software, financial tracking tools, and management reporting structures, companies can generate timely and accurate financial reports that support decision-making and improve operational efficiency. Whether it’s analyzing cost variances for hitches or monitoring cash flow for concrete grinders, internal reporting systems provide manufacturers with the insights they need to optimize their financial performance and achieve their strategic objectives.
Regulatory compliance is a key consideration for manufacturers, as companies must adhere to applicable accounting standards, tax regulations, and financial reporting requirements to ensure legal and ethical business practices. By staying informed about changes in accounting regulations, maintaining accurate financial records, and submitting timely reports to regulatory authorities, manufacturers can demonstrate compliance and mitigate the risk of fines, penalties, and reputational damage. Whether it’s preparing financial statements for fire protection sprinkler companies or reporting on tax liabilities for home builders, manufacturers must prioritize regulatory compliance to protect their business and uphold their reputation.
8. What Are the Best Practices for Handling Procurement and Supply Chain Finances?
Procurement and supply chain finances play a critical role in the financial health and operational efficiency of manufacturers, as companies must manage costs, optimize supplier relationships, and enhance supply chain visibility to drive profitability. By adopting best practices for supplier negotiations, cost analysis, and contract management, manufacturers can maximize value, reduce risks, and improve collaboration with their supply chain partners. In this section, we explore the best practices that manufacturers use to handle procurement and supply chain finances effectively.
Supplier negotiations are a key component of effective procurement management for manufacturers, as companies must establish mutually beneficial relationships with suppliers, negotiate competitive pricing, and secure favorable terms to optimize costs and ensure quality. By conducting supplier assessments, setting clear performance expectations, and negotiating value-added services, manufacturers can build strong partnerships that drive innovation and deliver long-term value. Whether it’s negotiating pricing for stainless steel clamps or securing delivery schedules for high-pressure hermetic seals, effective supplier negotiations are essential for manufacturers to control costs and maintain a competitive edge.
Contract management is a critical function that manufacturers must prioritize to ensure compliance, mitigate risks, and maximize the value of supplier contracts. By developing contract management strategies, establishing performance metrics, and monitoring contract compliance, companies can minimize contract disputes, improve supplier relationships, and drive operational excellence. Whether it’s negotiating service agreements for hitches or managing procurement contracts for rebar fabrications, effective contract management practices enable manufacturers to optimize their supply chain operations and achieve sustainable growth.
9. How Do Manufacturers Leverage Technology for Financial Efficiency?
Technological innovation plays a key role in helping manufacturers enhance financial efficiency, improve operational performance, and drive growth. By automating financial processes, leveraging data analytics, and integrating ERP systems, companies can streamline operations, reduce costs, and optimize resource allocation. In this section, we explore how manufacturers leverage technology to achieve financial efficiency and competitive advantage in today’s digital age.
Automating financial processes is a key strategy that manufacturers use to streamline routine activities, reduce errors, and improve efficiency. By implementing automated accounting systems, invoice processing software, and payment processing solutions, companies can accelerate transaction processing, improve data accuracy, and enhance process transparency. Whether it’s automating invoice approvals for heavy equipment sales or streamlining expense reporting for intrinsically safe barriers, automation technology enables manufacturers to save time, reduce costs, and focus on strategic initiatives that drive growth.
ERP systems integration is a critical component of technology adoption for manufacturers, as companies must seamlessly connect their financial systems with other business functions to improve data visibility, streamline processes, and enhance collaboration. By integrating ERP systems with accounting software, inventory management systems, and supply chain platforms, manufacturers can achieve greater operational efficiency, real-time reporting, and decision-making capabilities. Whether it’s integrating financial data for fire protection sprinkler companies or aligning production schedules for rebar fabrications, ERP systems integration enables manufacturers to unlock the full potential of technology and drive financial efficiency across their organization.
10. How Do Top Manufacturers Approach Sustainable Financial Practices?
Sustainability is an increasingly important consideration for manufacturers, as companies must balance financial performance with environmental responsibility and social impact. By aligning financial goals with sustainability objectives, investing in green technologies, and reporting on ESG (Environmental, Social, Governance) metrics, manufacturers can demonstrate their commitment to sustainable practices and create long-term value for their stakeholders. In this section, we explore how top manufacturers approach sustainable financial practices to drive positive impact and secure their future.
Aligning financial goals with sustainability objectives is a strategic approach that manufacturers use to integrate environmental and social considerations into their business operations and decision-making processes. By setting sustainability targets, measuring performance against ESG metrics, and aligning incentives with sustainability goals, companies can enhance their reputation, attract socially responsible investors, and drive long-term value creation. Whether it’s reducing carbon emissions for home builders or implementing waste reduction programs for concrete grinders, aligning financial goals with sustainability objectives enables manufacturers to mitigate risks, seize opportunities, and build a more sustainable future.
Investing in green technologies is a key strategy that manufacturers use to reduce their environmental footprint, improve resource efficiency, and drive innovation. By embracing renewable energy sources, implementing energy-efficient technologies, and adopting sustainable manufacturing practices, companies can reduce costs, lower emissions, and enhance their competitiveness. Whether it’s deploying solar panels for fire protection sprinkler companies or investing in energy-efficient equipment for rebar fabrications, green technology investments enable manufacturers to achieve environmental sustainability goals and create value for their business and society.
Conclusion
In conclusion, financial management is a critical aspect of the success and sustainability of manufacturing companies across various industries, from metal etching stencils to concrete grinders. By employing effective financial strategies, maintaining cash flow, leveraging technology, and embracing sustainable practices, top manufacturers can navigate the complexities of the financial landscape and achieve long-term success. By prioritizing financial efficiency, innovation, and sustainability, manufacturers can create value for their stakeholders, drive growth, and secure a competitive advantage in today’s dynamic business environment.