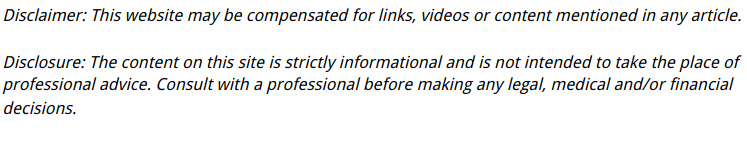
Although many industries are vulnerable to rapidly changing market environments, the oil and gas industry is one of the most unstable. It’s no surprise that you could buy gas today, and three days later, the price is up by 20 cents. Although the oil and gas industry is one of the most profitable, challenges such as political instability, market fluctuation, shortage of steel supplies, and aging equipment put a cap on profit and business sustainability.
Because of unpredictable market environments, oil companies often cut costs to avoid losses. Repair and maintenance (R&M), labor supply, and commitment to net zero are often the business aspects that experience budget cuts. Yet this can hurt business in the long run. According to Automation, a typical oil and gas facility experiences losses of $22,000 per hour, 32 hours a month, because of unplanned downtime.
Offshore oil rigs have unique circumstances that necessitate engaging commercial contractors who offer offshore oil rig maintenance services. For example, fluid composition changes can affect equipment’s corrosion rates. Some jack-up rigs have existed for over 40 decades and require repair and maintenance. So, it makes the most sense for oil companies to invest in their businesses through offshore oil rig maintenance services.
Trends in the Oil and Gas Industry
Recent trends in the oil and gas industry, especially offshore rigs, necessitate investing more in offshore oil rig maintenance services. Here are five trends that will inform how oil companies operate and respond to emerging issues.
1. Increased Oil Prices and Energy Transitions
Although oil companies have experienced low fuel prices for a long time, things might be changing for the better. According to a Times article, the Russian invasion caused a sharp increase in oil prices, one of the highest in the oil market, with some companies enjoying as much as a 48% boost in profit.
Increased oil prices should ideally enable more investment in cleaner energy solutions such as carbon capture, utilization, and storage. Players in the value chain, including offshore rig maintenance services, have a critical role in this transition.
2. New Era in Energy
As more attention goes to climate change, a new era in energy is emerging. Masses are angered by massive and deadly accidents in oil rigs. Modern technologies such as NH3 control systems have helped mitigate such incidences, but proper training, regulation, and regular maintenance are critical.
For oil companies to stay afloat and relevant in the new energy era, their business model must shift from the conventional oilfield business and offer integrated solutions such as subscription-based revenues. Oil companies must embrace greener and leaner technologies and digitize operations.
3. Changing Preferences in the Market
Whole markets are experiencing shifts as more millennials have purchasing power. Millennials with different preferences will influence how oil companies operate in the next decade. Oil companies might need to brand and re-brand themselves as businesses offering convenience and a customized user experience. Of course, in the long run, oil companies might have to offer more than fuel to stay engaged in this market.
4. Poor Labor Retention Leading to Talent Loss
Although the oil and gas industry is one of the most valuable, it also has one of the poorest retention rates. Even after the price recovery in 2022, many jobs have not been recovered. According to Deloitte, only 50% of lost jobs have been recovered.
Instability in labor retention could lead to talent loss with significant implications for oil companies. Jobs along the value chain, including offshore oil rig maintenance services, are at risk. Oil companies can use flexible and agile labor systems to compete in the tight labor market.
5. Intensified Push Towards ESG Practices
Stakeholders in the oil and gas industry are looking for more than financial incentives. Proper ESG practices are becoming more and more critical. For oil companies interested in mergers and acquisitions, an ESG-friendly portfolio will be essential. One of the ways to have a portfolio that stands out is by engaging in efficient offshore oil rig maintenance services.
Why Maintenance Is Essential
During low price cycles in the oil industry, oil companies often cut down on maintenance and supply budgets. External factors such as supply-chain challenges in the steel foundry industry can make maintenance seem quite expensive. For cash-strained oil companies, maintenance may seem unnecessary.
Yet maintenance, for example, through a planned preventive program, offers numerous advantages for offshore rigs. Here are some of the reasons oil companies must engage offshore rig maintenance services:
For Safety Reasons
According to the Census of Fatal Occupation Injuries, 489 workers in the oil and gas industry died between 2014 and 2017. While some accidents are not related to maintenance, aging equipment and poor maintenance cause such accidents. Putting maintenance on hold might save some money quickly, but no human loss is worth any monetary gains.
Imagine a rig contractor putting industrial welding on hold for a loose fitting or a wobbly rail and harming a worker. The cost of human life will be more costly. So, oil companies must engage offshore rig maintenance services to ensure worker safety. Offshore oil rig maintenance also reduces environmental incidences, such as fires that injure workers in rigs. An NH3 control system also comes in handy to prevent potential hazards of ammonia to workers and marine life.
Reduce Company Costs
Proactive rig maintenance will help an oil company avoid human life, time, and capital costs. For example, marine diesel surveying will highlight problems before they arise. Workers are left with unplanned downtime when a piece of equipment or vessel breaks down and operations cease. Repairing the failed equipment will cost the company more than preventive maintenance.
Improved Drilling Performance
Poor or malfunctioning aspects such as loose hoses and fittings will only slow down performance. Workers may have to temporarily stop production from fixing a fitting, sometimes putting themselves at risk. Even when the work pauses are short, they interrupt performance and production. Engaging offshore oil rig maintenance services ensures efficient and improved drilling performance.
Increased Efficiency
If a machine breaks down during work hours, the scrap materials are unplanned; thus, even after maintenance is done, the process will be inefficient. Production delays also cause late shipments and increased material and labor costs. Lack of proper maintenance will only cost companies and sometimes cause massive losses in profit.
Typical Areas Requiring Maintenance
While almost every aspect of an offshore rig needs maintenance, some areas might need more regular maintenance. Here are some of the areas requiring regular assessment:
- Electrical, Control & Instrumentation: Some electrical components are used beyond their life span or after becoming obsolete. Yet poor functioning could cause fires or slow down performance.
- Pipelines: Pipelines are prone to corrosion because of harsh marine conditions. Maintenance may include powder coating and welding leaking places. Fluid compositions may also change, hence increasing corrosion rates. Other external conditions may cause cracking.
- Cranes and Lifting Equipment: Weak joints and changes in operating conditions and loading necessitate maintenance and repair. Lifting equipment may have loose fittings because of intense and regular movement. Joints and bearings require oiling to work in optimum conditions.
- Telecommunication may include electrical components, but all telecommunication equipment requires regular assessment to ensure they are in working condition. Telecommunication equipment is essential during emergencies, so it should always be in good condition.
- Marine Systems Including Engines: Even without the harsh marine environment, engines require maintenance. Maintenance may include oil sample testing, checking internal components, and changing fuel filters. Hydraulic service is essential to ensure pressure control systems work at optimum levels.
- Fixed Offshore Structures: Offshore fixed structures may degrade over time. Offshore oil rig maintenance services ensure components such as k-joints work through asset life extension. Industrial doors, too, may need oiling at the edges. Large desalination plants require cleaning and asset inspection for rusting.
Strategic Approaches Oil Companies Can Use in Maintenance
Oil companies use different strategies when it comes to maintenance; some are proactive, and others are reactive. Each has an impact on business outcomes. Here are five common approaches to maintenance in the oil and gas industry.
1. Reactive Maintenance
The least labor-intensive approach is letting equipment run to failure. For example, allowing an engine to run until it can’t work anymore. Some equipment will naturally cease working without maintenance and can only be used as scrap material.
Sometimes, it may make economic sense to let some equipment run to failure, especially if it is a non-critical asset. However, it might be problematic to let equipment such as marine engine run to failure. It may also not make sense to let assets with a significant impact on sustainability run to failure.
2. Scheduled Preventive Maintenance
Planned preventive maintenance is a recommended strategy with multiple benefits, including less downtime, cost-saving, and safer working conditions. Rig contractors schedule maintenance based on time or usage intervals. For example, maintenance might be monthly or after three cycles of usage.
Although planned maintenance can offer immense benefits for an oil company, it has drawbacks. Scheduling maintenance is based on company guidelines that may not be exact because of a lack of contextual information. You could be erroneously over-maintaining or the opposite. Planned maintenance may be challenging for companies with poor access to their data.
3. Asset Condition-Based Maintenance
Conventional engineering wisdom calls for asset life extension. For example, a company may engage offshore oil rig maintenance services for asset life extension of their fixed offshore structures. Yet sometimes reliability is a significant factor for consideration.
Reliability-centered maintenance aims at increasing the productivity of equipment and not necessarily its asset life. Through condition-based maintenance, maintenance and reliability, technicians use analytics to understand the current status of an asset’s functionality.
4. Predictive Maintenance
Predictive maintenance aims to keep assets in optimum condition, increase work lifecycles, and avoid costly maintenance – unlike preventive maintenance, which is scheduled at intervals. Predictive maintenance is scheduled based on the asset’s condition.
Predictive maintenance uses preventive and condition-based maintenance methods to track asset performance. PM aims to identify problems early on and prevent expensive maintenance activities. With modern technologies such as IoT, companies can use software dependent on machine learning to pick signals on equipment’s health.
Predictive maintenance reduces maintenance costs while ensuring the process runs at optimum capacity. Data access is essential in predictive maintenance since it relies on machines to use historical data to make predictions. Engineers can use such software to sift through massive amounts of data to make informed decisions on maintenance.
5. Dynamic Maintenance
The long-term direction in oil rig maintenance is dynamic maintenance. It is an approach that uses all of the above-mentioned approaches, both proactive and reactive. Dynamic maintenance optimizes operational maintenance costs and asset management through incremental improvements in maintenance plans. It is not a widely incorporated strategy but the direction oil companies are headed.
Final Thoughts
The oil and gas industry has been through some events that caused instability. Yet recently, oil prices have shot up, promising profit recovery. A significant portion of offshore rigs is at least 40 years old. Many require general maintenance.
The recent increase in the oil price should encourage and enable oil companies to engage in offshore oil rig maintenance services. Maintenance will reduce losses in downtime, human life, and equipment damage. If anything, maintenance should be a mandatory and regular process in ESG-compliant oil companies.
Oil companies should move from conventional reactive maintenance to preventive and proactive maintenance. Ultimately, oil companies should incorporate all the different maintenance approaches through dynamic maintenance. Now is the best time for oil companies to invest in their business by engaging in offshore oil rig maintenance services. Oil prices are high, and the market demands optimum production.